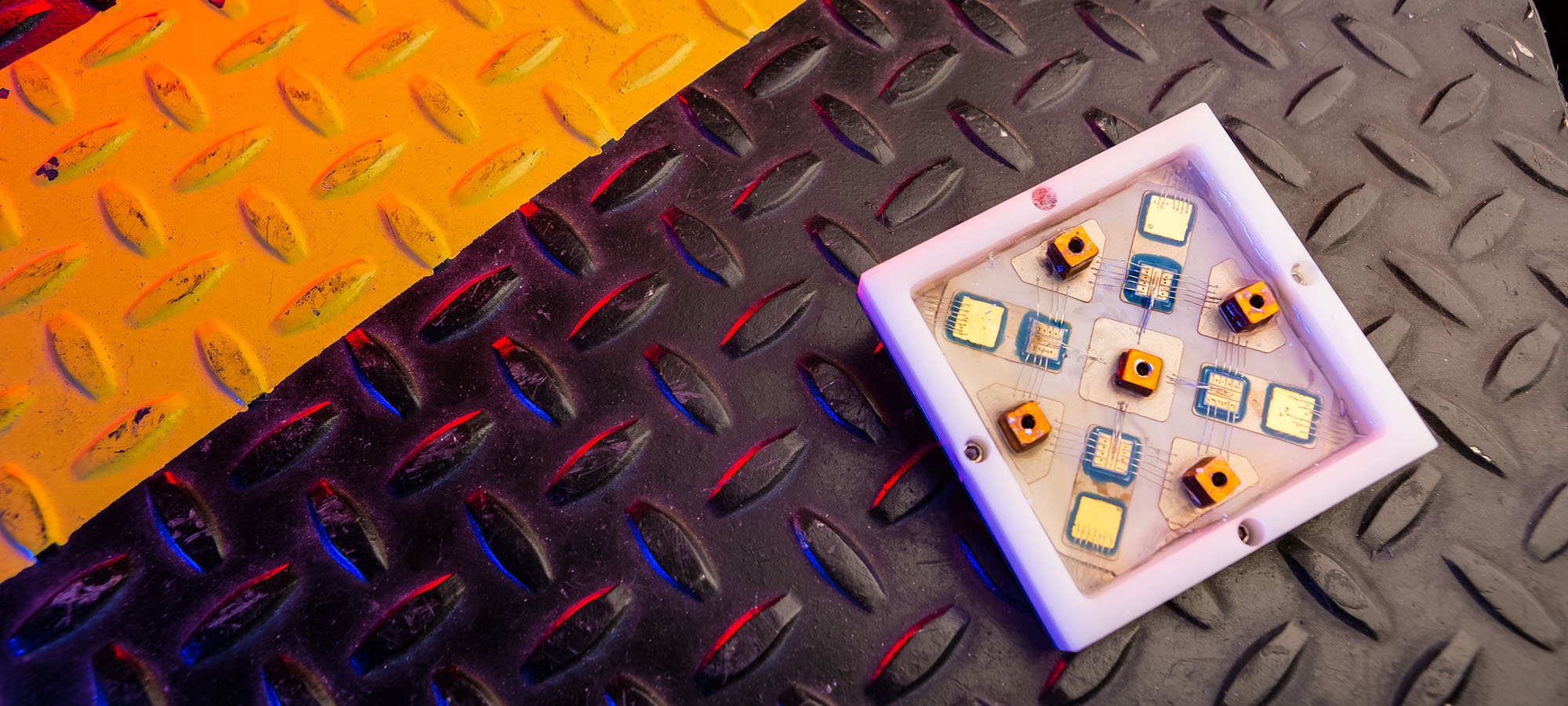
No Shortage of Innovation
Anyone recently shopping for a new or used car has undoubtedly experienced the shortage in available automobiles. One contributor to this is the decreased availability of semiconductors and chips, which are required to maintain the level of electronification and automation in cars today.
Alan Mantooth, distinguished professor of electrical engineering and part of the University of Arkansas Power Group, notes that no fewer than 25 chips are used in the manufacturing of new vehicles.
The U of A Power Group consists of world-class faculty experts in power and energy
research, spanning engineering and science disciplines, jointly working to deliver
next-generation electric vehicles, renewable energy systems, grid infrastructure and
cybersecurity. Within the group, Mantooth’s specialties focus on semiconductor device
modeling, CAD, packaging, power and analog IC design and cybersecurity.
“These chips need to be more resilient, so we’re researching how to pack them in closer and take more heat,” he says. “When they’re smaller, they can be put into more places. This is where silicon carbide comes in.”
Mantooth leads a team of engineering researchers who, in 2021, received nearly $18 million from the National Science Foundation to build and operate a national silicon carbide research and fabrication facility at the university. It will be the only facility of its kind in the nation.
Another $5.4 million in total funding from the Army Research Office and the Army
Research Laboratory was awarded in 2021 for use toward equipment, student and staff
compensation, tuition, and materials for collaborative research activities with the
new silicon carbide semiconductor fabrication facility and the Army Research Lab.
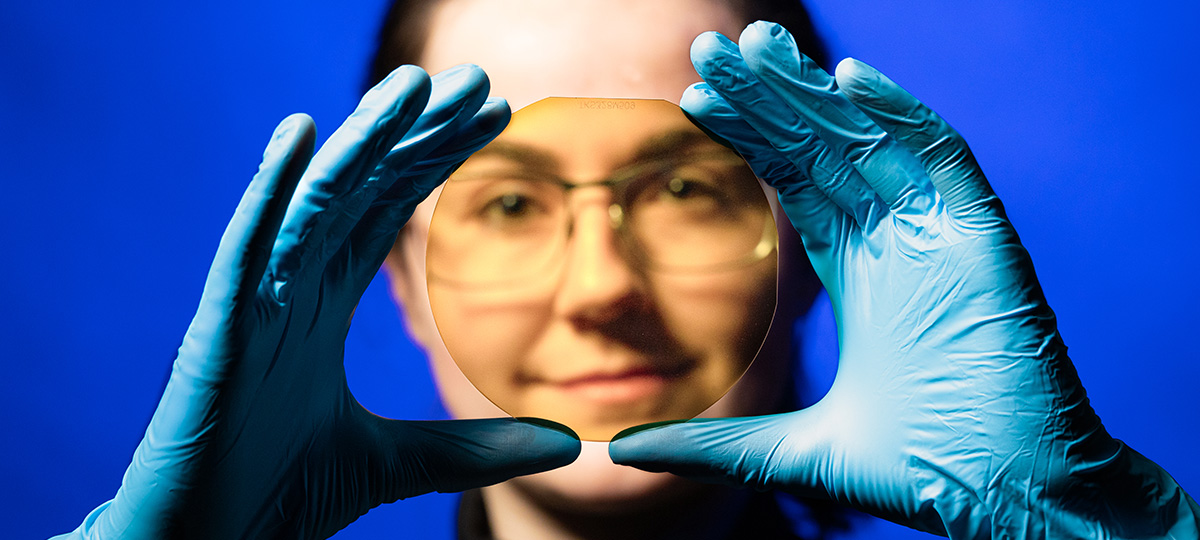
“The national impact of having a fabrication facility such as this is enormous,” Mantooth said. “The country that leads the world in advancing silicon carbide semiconductor design and fabrication will also lead the race to market nearly all new game-changing technologies, including those used by the military, as well as general electronic devices that are essential to our economy.”
“The country that leads the world in advancing silicon carbide semiconductor design and fabrication will also lead the race to market nearly all new game-changing technologies, including those used by the military, as well as general electronic devices that are essential to our economy.”
It was a dream years in the making, as the University of Arkansas Power Group posited the idea of a facility that could produce silicon carbide components. These components, which until now were fabricated abroad, are used in a variety of electronics, sensors and optical devices. Now, though, the U of A will offer the only facility in the country to test low volume fabrication for manufacturers that eventually want to ramp up their production.
"This provides a key pathway to higher volume products for the next generation of power electronics, extreme environment electronics, and high power density systems for applications such as more electric transportation including passenger vehicles, trucks, heavy equipment, and aircraft," Mantooth said.
Mantooth and other U of A electrical engineering researchers have decades of experience working with silicon carbide. They are one of only a few university research groups capable of developing integrated circuits with the powerful semiconductor. Combining this expertise with cutting-edge equipment and infrastructure will enable the production of superior integrated circuits for lighter and faster electronic systems, which will also be more energy efficient and heat resistant.